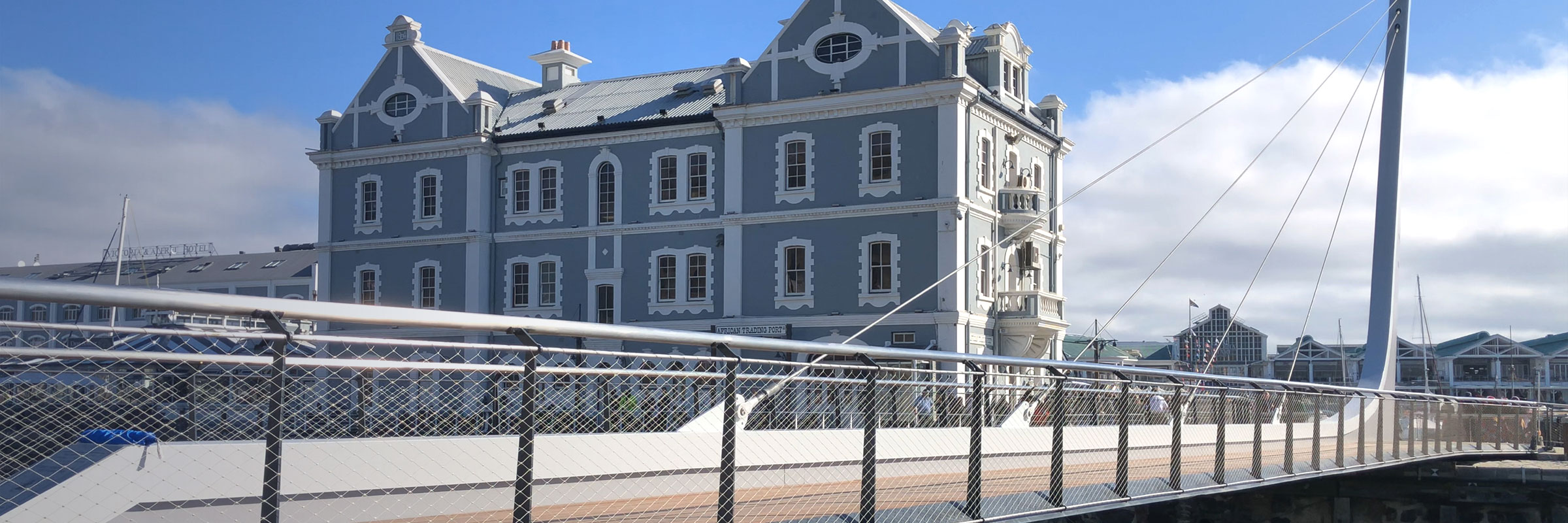




Leveraging technical expertise to identify fit for purpose solutions
The design team worked through various options for the new link. Among those considered were a bascule and lift bridge; however, it was deemed that a swing bridge would still be the best solution in terms of the speed of operation and electrical energy needed to operate it. Important performance specifications included the bridge being capable of operating in wind speeds of up to 60 km/h, that it be designed for impact by a vessel from both directions and swing free in such an instance so as to protect the mechanical equipment.
Both steel and Fibre Reinforced Polymer(FRP) were considered at the early stages of the project as the only materials that were light enough to limit the loads on the moving mechanical parts and to limit the foundation size. However, as the design progressed the use of steel was the obvious choice.
The new 4 m wide swing bridge has a span of 40 m. The deck is cable-stayed with a single plane of four locked coil cables connecting to a central, upstand spine beam. The spine beam is 500 mm wide and has a total depth of 800 mm, but only 470 mm protrudes above the top of the deck. The reclining pylon is in the continuity of the main central beam and its stiffness transfers the cable loads into the piled substructure. The steel with timber deck is rotated on a slewing bearing, which is stressed down onto a doughnut-shaped pile cap by 34 vertical Freyssibars. The bridge is supported on eight piles, positioned in a ring.
The slew bearing and hydraulic motors are in a plant room, created by the pile cap ring. By forming the pile cap in this way, it was possible to house the mechanics within the depth of the foundations. This reduced the required excavation depth and kept the foundations above sea level, which was advantageous from a durability perspective. It also limited the construction impacts on the historical quay wall.
A slew bearing option was preferred as it was considered to offer a more sustainable solution. Slewing bearings are tried and tested in both pedestrian bridge and industrial applications. Their large diameter allows them to resist overturning moment and hence a cable stayed bridge with no backstays could be conceived. This was attractive in that it limited the works that had to be done on the quayside. It also allowed the bridge superstructure to be fabricated and assembled off site and then barged and lifted into place, complete, on a single day.
Industry recognises outstanding project outcomes
The project, which was delivered within very tight commercial and time constraints, were split into two stages to ensure that construction works did not run into the V&A’s peak periods. The piling works was first built under one contract and then buried in sand and the area re-paved until the superstructure contract was activated the following year.
The Project Team together with the V&A Project Managers put significant thought and effort into minimising disruption to the area. Safe access across the cut for the public was maintained using the old swing bridge for all but four weeks of the construction works – a major achievement that required innovative thinking and expertise. The new V&A Waterfront swing bridge was officially opened to the public on 11 July 2019.
In 2020, the project was named joint winner in the Technical Excellence category of the South African Institute of Civil Engineering (SAICE) National Awards, 2020. It also won both the Bridges category and was recognised as the Overall Winner (across all categories) at the Southern African Institute of Steel Construction (SAISC) Steel Awards, 2020.