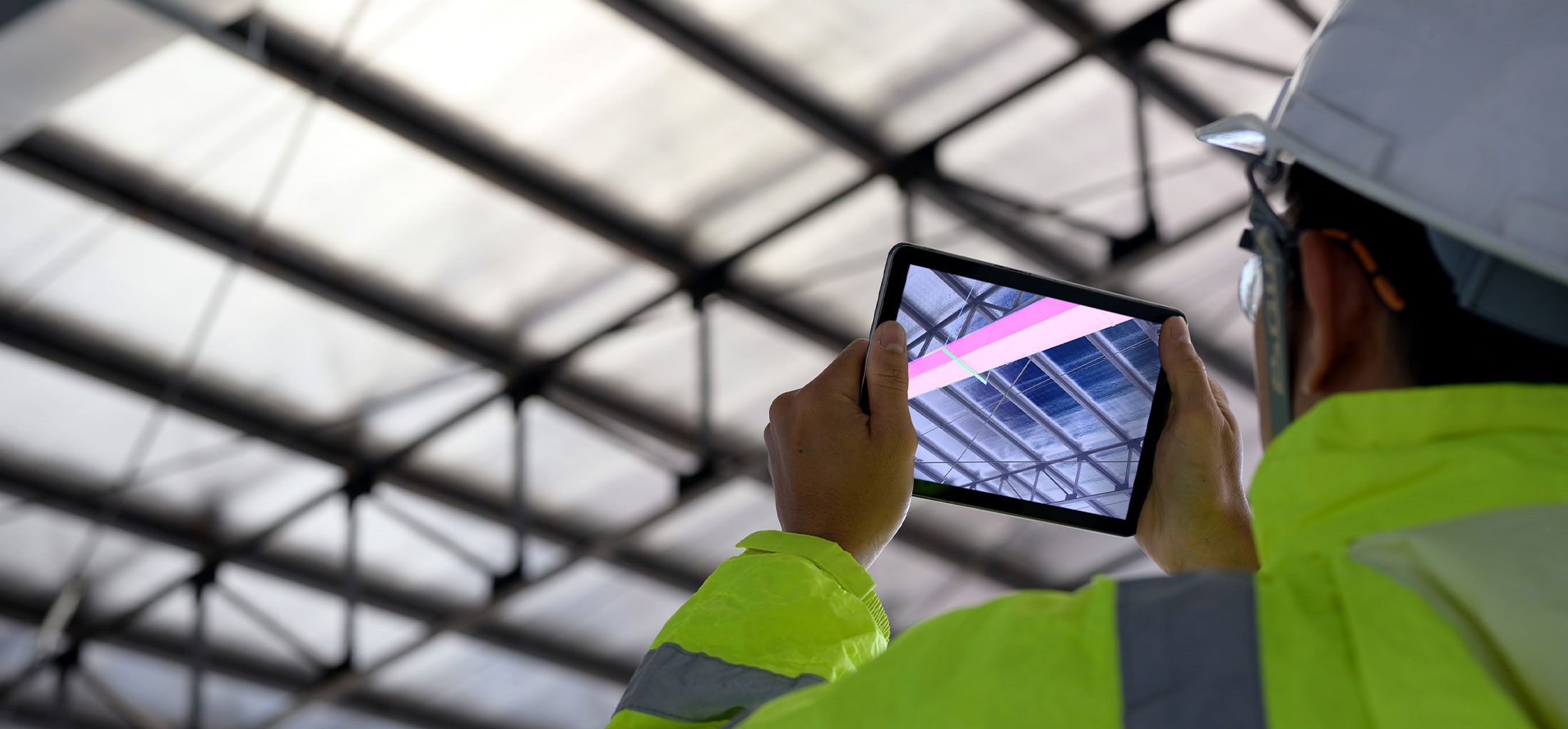
Circular Economy in the Built Environment
In 2023, Chalmer’s University of Technology in Gothenburg released four high level principles on introducing a circular approach in the built environment in their journal article ‘Developing regenerate: A circular economy engagement tool for the assessment of new and existing buildings’.
Model developed by Chalmers Technical University to indicate the four high level principles for circular building
Design for Adaptability
Examines how the infrastructure in a project can be adjusted in the future to prolong the lifespan of the project’s infrastructure, while preserving materials at their highest value.
Design for Deconstruction
Considers how a project can be deconstructed at the end of its life. This principle embraces modular design concepts that facilitate effective deconstruction.
Circular Material Selection
Considers how materials are selected to ensure maximum circularity. This principle promotes the selection of incorporating reusable components and recyclable materials instead of relying solely on virgin resources.
Resource efficiency
Explores how the project can be undertaken by using the fewest possible resources and generating minimal waste through embracing dematerialisation and industrial symbiosis. Highlighting the importance of efficient design and the selection of reused components and recycled materials to design out waste.
Moving forward the process of designing new infrastructure or housing for the advancement and construction of our built environment requires engineers and designers to consider and prioritise building for long-term use and future adaptability. This involves designing for longevity, adaptability, modularity and deconstruction, whilst also ensuring building utilisation and implementing policies for circular procurement in construction.
How do we measure Circularity?
Numerous qualitative and quantitative methods for assessing Circular Economy (CE) exist in today’s market. SMEC’s Circular Economy team is dedicated to aiding clients in gathering the necessary data to form a baseline. A good start when wanting to establish a baseline is to undertake a Material Flow Analysis (MFA) to measure the material flow for each project or building project and categorising these flows in terms of their connection to energy, water, and waste consumption.
There are several tools for measuring circularity on the market, the Ellen McArthur Foundation has indicated that harmonisation is important and will be discontinuing their Circulytics tool, instead referring to European Sustainability Reporting Standards (ESRS) which is embedding Circularity principles and future ISO Standards. Ultimately, there is not one tool which fits all but there is one tool or standard for all.
Leveraging BIM to implement Circularity
BIM extends beyond its use as a noun to denoting a 3D digital model. It equally describes the process that encompasses the creation, management, and utilisation of these models throughout a project’s lifecycle.
BIM goes beyond 3D models as a holistic approach that utilises technology and collaboration to improve efficiency and effectiveness across an asset’s lifecycle. Incorporating diverse data, or metadata, traditionally supporting design, construction, and asset management activities.
More recently BIM has been used to help measure a project’s sustainability rating, as part of the Infrastructure Sustainability Council (ISC)’s IS rating scheme which assesses the Sustainability performance of Infrastructure. Some of the various measures include environmental impact, community engagement, resource efficiency, and project management.
SMEC provide metadata connected to model elements that assist in capturing the performance of infrastructure projects. Taking a step further BIM can be leveraged to assess the circularity of projects, asset portfolios, or programs of works through structured metadata. Just as BIM aids sustainability, it can also facilitate the application of circular economy principles.
Metadata that aligns with circular economy principles is defined as pavement (e.g. material, recyclable content, expected decommissioning date, removal method, storage method) and plant and equipment (e.g. product, circular procurement, expected decommissioning date, hazardous material, end-of-life use including reuse, refurbish, recycle, and landfill).
By utilising BIM and standardised metadata, circularity improvements can be fostered. Projects and organisations can collaborate by sharing standardised metadata, fostering “Industrial Symbiosis”. This practical application of circular economy principles involves sharing resources, waste materials, energy, and expertise to create mutually beneficial relationships and to design out waste.
BIM, as a process offers a pathway to integrate circular economy principles seamlessly into infrastructure projects. Through collaborative efforts and strategic use of metadata, our projects’ sustainability and circularity can be elevated, contributing to a more resource-efficient and resilient built environment.
The Benefits
It is feasible to achieve a reduction of environmental impacts ranging from 40 to 90% by employing traditional materials and modular design approaches within the construction process. Beyond reducing the pressure on earth’s resources, reducing greenhouse gas emissions and increasing liveability, there are additional compelling reasons for construction projects to adopt a circular economy mindset.
Circular economy in construction should additionally be pursued to:
Align with Global Principles:
Embracing circular economy strategies in construction aligns harmoniously with the United Nations principles, Environmental, Social, and Governance (ESG) principles, as well as broader sustainability strategies and policies.
Attainment of Certification Standards:
Pursuing circular economy practices allows for the achievement of certification standards like the ISC and Green Building certifications. Often, construction sites are required to adhere to these standards, which encompass metrics such as recycled content and material choices.
Cost Savings:
Products utilising recycled content and/or sustainable aspects such as low energy usage/waste usage may cost more initially though long-term there is a value. Similarly applying a circular design approach may seem harder and take longer time to develop as the concept is new, the rewards are noticeable later on.
Looking towards the future there needs to be a shift from the current linear to a circular built environment. Incorporating the four high level principles for circular building, alongside the 10Rs of a circular economy and leveraging the Building Information Modelling (BIM) system can help facilitate this crucial shift across the lifecycle of our infrastructure assets.
By actively embracing these principles and taking concrete steps, we can contribute significantly to the transformation of our built environment into one that is more sustainable, adaptable, and circular. This not only critical for our environment but enhances the quality of life for our communities and generations to come.
References
Keck, E. (2017, February 22). The 20th century saw a 23-fold increase in natural resources used for building. CSIROscope. https://blog.csiro.au/the-20th-century-saw-a-23-fold-increase-in-natural-resources-used-for- building/#:~:text=As%20we%20noted%2C%2070%25%20of%20the%20buildings%20and
Gillott, C., Mihkelson, W., Lanau, M., Cheshire, D., & Densley Tingley, D. (2023). Developing regenerate: A circular economy engagement tool for the assessment of new and existing buildings. Journal of Industrial Ecology, 27(2), 423–435. https://doi.org/10.1111/jiec.13377
Circulytics – A world without measurement doesn’t work. (2023). Ellenmacarthurfoundation.org. https://ellenmacarthurfoundation.org/resources/circulytics/overview
First published in Sustainability Matters, October 2023.